Running 50Hz motor at 60Hz power system
2015-05-17
For some electric motors you can find needed circumstances such as voltage and bearing life time and lubrication services and achieved output power on motor plate and probably in motor manual. Normally you can obey from V/Hz constant and constant upper output power limit law with some acceptable error like variable speed scalar drive fed motors. For example a 400V 50 Hz 3 phase motor can work with 480V (in practice a little lower) and lower load torque for constant output power (Pm= T(torque)*W(speed)). But some manufacturers says that their product work with higher load torque and output power in higher speed (frequency) this is an option and special advantage of a electromotor.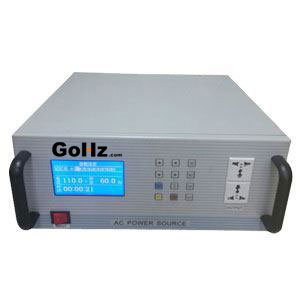
We have been running motors above base speed since VFDs were introduced. I have run small motors up to 4 times base speed in demonstrations - then I chickened out. Most good motors are rated to run 50% over speed without damage. The OLR will protect it. 20% higher speed at 60Hz is likely to damage the motor and pump; assuming V/Hz are equal.
I'm sure the pump bearings won't be damaged by 20% over speed form 50Hz to 60Hz. The torque requirement will increase but again there is an OLR for protection. I doubt that the pump will mind. You can do that but you must to check the nameplate for your reference because the motor current increases and the motor speed increases also. So, if the actual motor current is more than rated current (see on nameplate) you must to decrease the load.
The current will increase but that doesn't mean that it will exceed FLA; it may be lightly loaded. He didn't say this was a new motor on an existing pumping system so we still have a lot of questions. It almost sound like a pump with a 50 Hz motor on it and wants to run it on a 60Hz power supply. Or maybe he got a new machine with an IEC motor on it; who knows.
Most likely you will find that the motor nameplate will show data for both 50 and 60 Hz, if it is for a small pump. In general there should not be any major problems. The most important thing to check is that the current does not exceed the nameplate current when running 50 Hz motor at 60 Hz, as that could cause overheating of the windings.
Only recommended if voltage change is proportional. Speed will increase, Torque will decrease. If your pump is running at full capacity at 50 Hz this will be detrimental to the motor when you connect to 60 Hz power supply (being a variable load application).
There seems no problem in running a 50 Hz motor on 60 Hz. If it is driving a pump, heating may increase but it will be taken care by increase in fan speed. Pump discharge more pressure which may be controlled by throttling discharge valve. If the voltage is increased in proportion, then speed AND power will increase, for the same current. The torque is what stays the same, for the same current. A minor increase (<20%) in iron losses can be expected, but increased speed of the cooling fan will easily take care of this.
If I increase speed by 20% on a centrifugal pump or fan, the torque requirement will increase by 44% and Kw requirement will increase by 73%. That's why it's not practical to try to go over speed on a variable torque load. Constant torque is linear. Motor RPM will be higher than specified for 50 Hz may reduce life of motor, question is will the load handle the higher motor shaft speed at 60 Hz power system.